Headlining part three of my Clean Show coverage is my presentation of Sankosha’s new single-buck shirt unit and their new companion Collar/Cuff press. At first glance, this new unit dubbed LP-5600U, looks like many other Sankosha shirts except for this….
I’ve been writing this column for well over 20 years. I have not been covering the Clean Show like this for quite that long, but close. I’m not sure what made me feel like it is my responsibility to cover the show this way (probably writers’ block, honestly), no one at this publication ever asked me to do so. Anyway, back in those early days, I would ask each shirt unit manufacturer to show me only their new shirt unit; the one being introduced at the Clean Show for the first time. Major upgrades to an existed unit qualified, so Unipress’ update to their Cyclone unit (see September 2022) would have counted as a unit that I would have covered. And there would be about 12-15 shirt equipment manufacturers, some of them so unheard of and so obscure, (and not connected to steam) that I did not even cover them. They got zero press time. As time went on, many units didn’t change every couple of years, so I began to cover every company, every time, just to remind readers of each company’s offerings. Good thing. Only one major shirt unit manufacturer introduced a completely new shirt unit this year.
I can’t help but wonder what my father or grandfather would think if they saw a modern shirt pressing machine. They look so different! They certainly don’t look like an old Ajax Classic! How could they not marvel at the intricate robotic movements of a sleeve pleat press? Or a passive mechanism that stretches a collar or pulls down on a back while pressing?
But no one could have imagined a body buck that can press a shirt in TEN seconds, and I never thought to ask Santa Claus for that either. But that is what the new Sankosha LP-5600U can do! Crazy huh?
Before we go on, check out the videos. You gotta see it to believe it. Point your smartphone camera on the QR codes to view the videos on my YouTube channel.
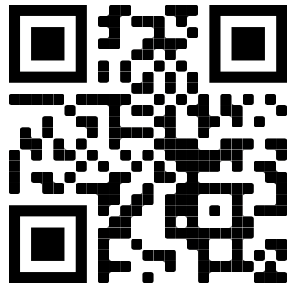
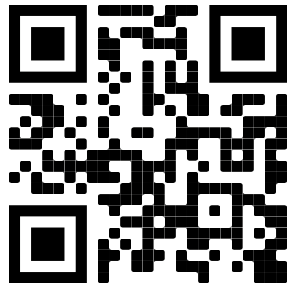
This unit is a game-changer. So fast is this unit, that they also had to invent a new collar-cuff unit that could keep up with it. That is the LP-6000U. It’s hard to explain how and why this unit works and it is difficult to get clear answers from Sankosha, so I must draw my own conclusions. So, what I am telling you here is my own summations, not official data.
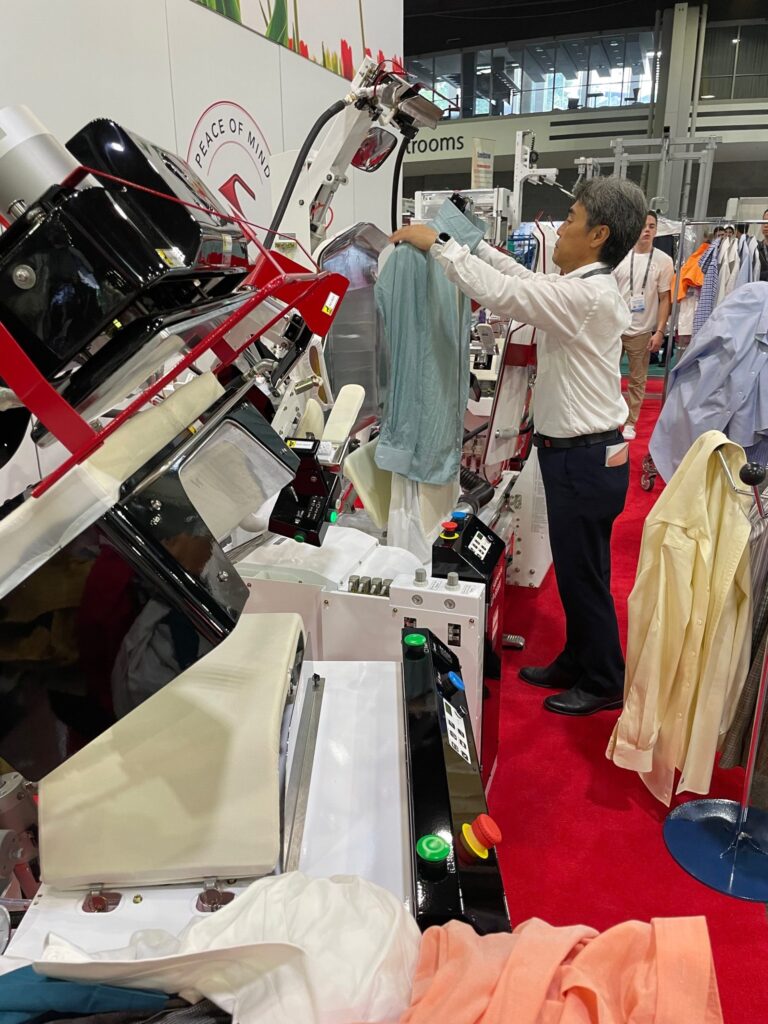
At first glance, the unit is not much different than previous models. You dress the buck in the traditional way. Then you move to the left sleeve (always the left sleeve first). The way the sleeve is attached assures a tight seal. Sankosha has done away with steam injection into the sleeves and added an additional heat exchanger. Therefore, the utility consumption nets out to be equal. When you actuate the left sleeve, the head moves over, and it moves close to the buck; but it stops about an inch away from the shirt. I think that this does two things; there is radiant heat that is pre-heating the water in the fabric. This must make a difference. Secondly, there is less travel remaining when the buck is indexed. It might seem like a small thing, no doubt, but that head will close onto the shirt in less than half a second. That matters! At many plants, the head needs to travel about 7-8 inches and that takes about 2 seconds. This is wasted time. When you actuate the right cuff, you do have the option to select a longer press cycle, but I pressed many shirts on this unit in Atlanta and never felt the need to do that. I never selected the long cycle, even once. The travel to the press position is very short and the head is closed in, literally, the blink of an eye. Faster than you can say “Holy Sankosha!” the cycle is done. There IS a bit of residual moisture on the pad side of the thick part of the heavier shirts. I don’t like that. But the shirt did continue to dry within a few minutes. Also, I am not aware of the moisture retention that they had in the shirts that they were pressing. If you are pressing 70-80 shirts per hour, which is what they are aiming for with one operator, you will want moisture retention on the lower side. I found that pressing on this unit was actually quite relaxing; enjoyable really. Can you really do 70 shirt per hour? Maybe. I wish that it had been possible to time myself. I was so busy fielding questions that I never got bogged down long enough for, say, 15-20 to see how many shirts I could do in that time. I think that the secret would be in the collar/cuff press. How fast can it be loaded. Once you send in the body buck, the cycle will be finished long before you’re finished loading the collar and cuff press. That certainly doesn’t mean that you can’t do 60, 70 or 80. I just don’t know what the number is.
The last shirt unit manufacturer that I’ll feature is PONY. Their equipment now has a feature that I asked for in December 2005!
If you’re an avid reader of this column, you may remember that in December of each year, I create a fantasy list to Santa Claus. This list is comprised of products or equipment, or equipment enhancements that, to the best of my knowledge, do not exist. I wish for them in this open letter to St. Nick, asking for them because I believe that these products would help us in our everyday business lives. As it turns out, a few of my wishes actually have come true. I can’t say for sure if I have actually inspired an engineer or two, but I’m just happy that some products have become better along the way.
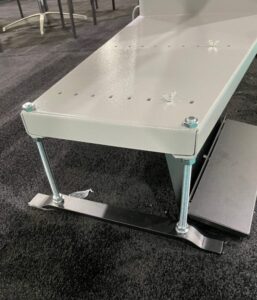
In December, 17 years ago. I thought that it would be a good idea if shirt presses could be raised or lowered to accommodate the different heights of, uh, let’s say… the vertically challenged members of your staff. I was thinking, if I remember correctly, a kind of hydraulic or pneumatic thing that would allow you to raise and lower your press, on the fly. Well, that would be costly, and that is not what PONY has done. They did something that no one else is doing. And its about time! On most of their machines, the leveling legs have a great deal of “meat” on them so that the bucks can be considerably higher or considerably lower when installed. And, if you don’t have rigid steam pipes in your area, changing the height for a new employee won’t take but a few minutes.
Until next month…

Donald Desrosiers
Don Desrosiers has been in the laundry and drycleaning industry for over 30 years. As a management consultant, work-flow systems engineer and efficiency expert, he has created the highly acclaimed Tailwind Shirt System, the Tailwind System for Drycleaning and Firestorm for Restoration. He owns and operates Tailwind Systems, a management consulting and work-flow engineering firm. Desrosiers is a monthly columnist for The National Clothesline, Korean Cleaners Monthly, The Golomb Group Newsletter and Australia's The National Drycleaner and Launderer. He is the 2001 winner of IFI's Commitment to Professionalism Award. He has a website at www.tailwindsystems.com and can be reached at tailwindsystems@charter.net or my telephone at 508.965.3163