Removal of non-volatile residue, dyes, and most odors from drycleaning solvents is most effectively achieved by distillation. Distillation is the process of purifying the solvent by converting it to a gas by boiling and then condensing the vapor to a liquid by cooling. This process takes place in a piece of equipment called a still. When distillation is complete clean solvent is returned to the drycleaning system and all the impurities are left behind.
Unlike perchloroethylene, petroleum solvent distillation is always conducted under vacuum. This prevents fire hazard, and at the same time lowers the boiling point of petroleum solvents. At higher temperatures, petroleum solvents tend to break down, which in turn causes the formation of unpleasant odors. The vacuum system eliminates this possibility.
Some newer machines are set up with more frequent distillation. This increased distillation of solvent is resulting in fewer complaints concerning solvent odor. Odor problems with solvents are not completely eliminated, however, and should not be ignored.
DISTILLATION OF PETROLEUM SOLVENT
There are two types of stills: batch and flash. The type of still is determined by how the solvent is introduced into the still.
In the batch still, the still is filled with the recommended amount of dirty solvent followed by heating to the desired temperature. The distillation will end once all dirty solvent has been distilled.
A flash still distills solvent continuously. A small quantity of solvent is intermittently pumped into the still from the dirty solvent holding tank. The distillation ends when the dirty solvent tank becomes empty.
Petroleum solvent boiling points range from 300° to 410°F. A vacuum still makes it possible to distill petroleum solvent at temperatures approximately 100 degrees lower than would be required at normal atmospheric pressure.
Regular Stoddard solvent usually requires steam pressure of 27–30 psi. Low Dry or Fast Dry Solvent can be properly distilled at a lower steam pressure of 24–26 psi. But 140°F solvent will distill properly at the elevated steam pressure of 31–32 psi.
With the introduction of higher flash point solvents, such as Exxon DF-2000, manufacturers recommend even higher steam pressures. These recommendations mostly affect the newer dry-to-dry petroleum machines that are built specifically for these high flash point solvents. The manufacturer’s recommendations should be strictly followed.
One of the main requirements for efficient distillation is to prevent the buildup of non-volatile residues in the still. Failure to periodically drain the still will result in slower distillation.
SOLVENT ODOR CAUSED BY DISTILLATION
Although one of the purposes of distillation is removal of most odors from the solvent, sometimes odors develop during the distillation itself.
The common cause of odors in petroleum solvent are:
1) WATER SEPARATOR
While periodic cleanup of the water separator is essential, it is important that the water in petroleum water separators be changed frequently. This is necessary because the water in the water separator is susceptible to the growth of bacteria.
REMEDIAL ACTION
- Tumble dry a load of cotton rags/towels to remove any residual moisture.
- Dryclean on a regular cycle, loading the machine to at least 50% of its rated capacity.
- Run regular cycle.
- Tumble dry at high temperature: 175–180°F.
- Smell towels, then take to a press and steam for no more than five seconds and check again for any residual odor.
- Wash towels in a wash formula with chlorine bleach.
- Tumble dry.
- Repeat steps 2–7 until the towels/rags no longer have an odor.
2) HIGH STEAM PRESSURE
This happens when the vacuum pump malfunctions. When there is not enough vacuum in the still, the temperature will rise, resulting in a boil-over causing components of dirty solvent to carry over with the distilled solvent.
REMEDIAL ACTION
Frequently check the vacuum gauge to verify that proper vacuum pressure is maintained in the still.
3) SMALL TRACES OF STAIN REMOVAL AND PRESPOTTING AGENTS
Sometimes a buildup of stain removal and prespotting agents will cause the solvent being distilled to foam and bring over undesirable impurities to the distilled solvent. All stain removal chemicals must be flushed completely from the fabric either with a volatile dry solvent or steam/water, and then dried before drycleaning.
REMEDIAL ACTION
To remove traces of stain removal agents, distillation must be done at a low steam pressure that allows only a very slow distillation. To remove excessive moisture, proceed to dryclean pre-dried all cotton rags or towels in a complete drycleaning cycle as described in the remedial procedure in problem No. 1.
4) CONDENSER LINT
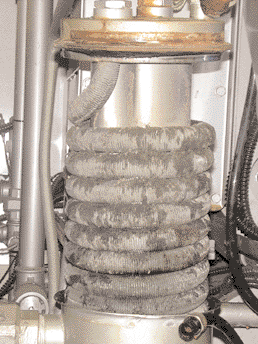
clean it immediately.
Odor caused by lint is the result of insufficient maintenance of the drycleaning machine. Lint on the condensing coils can cause sour or musty odors.
REMEDIAL ACTION
Clean condenser coil. In most cases the odor can be removed by redistilling the affected solvent. If this does not help, try running all cotton rags several times in the contaminated solvent per the remedial procedure described in problem No. 1.
5) OVERFILLING THE STILL
Overfilling the still is a common error. The result, in most cases, is that impurities will “boil” over. The still should be filled with dirty solvent up to the still manufacturer’s recommended level.
6) EXCESS MOISTURE IN SOLVENT
Excess moisture from moisture-containing prespotters, high relative humidity, or any water or steam leak can cause the solvent to boil over at normal operating temperatures. This is often caused by not pre-drying moisture prespotted garments.
7) NEW SOLVENT ODORS
There is always the possibility that some new solvents have an odor. Petroleum solvents, unless they are of the “odorless” type, have characteristic odors. Usually, they are a “sweet” type of odor. This odor will vary, depending on the source of the crude oil from which the solvent was manufactured.
However, petroleum solvents are more susceptible to develop an odor than perchloroethylene. A “sour” odor can develop in new petroleum solvent when it is stored for a long period of time.
CONCLUSION
The majority of objectionable odors caused by distillation can be avoided by conducting regular maintenance of the equipment. This way, even if we cannot avoid sudden objectionable odor occurrence in the plant, at least we will have control over the gradual build-up of bad odors in solvents.
Identification of objectionable odor and subsequent removal are sometimes difficult tasks. A general step-by-step guideline for what to look for is summarized below.
- Review your machine’s maintenance schedule.
- Ascertain that the recommended distillation rate is maintained. Check if boil-over of solvent occurred.
- Distill part of the solvent at the 20–40% of the recommended steam pressure. Collect a small amount of distilled solvent in the clean jar and perform a simple residual odor test. Immerse a clean, odorless cotton towel in the distilled solvent. Use the machine’s manual drying cycle to dry the towel. Once dried, smell the towel for odor, then steam it for no more than five seconds to check if there is any residual odor left. If not, distill the remaining affected solvent at the same low steam pressure. Regenerate spin filters and replace all cartridge filters. Clean the water separator thoroughly and add new solvent and water.
- If the slow distillation of affected solvent doesn’t help, run pre-dried cotton rags and/or towels several times in the complete cleaning cycle at the elevated drying temperature. Check for residual odor left after steaming a few rags.
This article is from DLI‘s TOI-690
