Let’s discuss three major types of boilers used in the drycleaning and laundry industry
Fire-tube boilers
The fire-tube boiler has its fuel gases pass through the inside of the tubes. The water surrounds the tubes and is heated by the burning gases. All fire-tube boilers will have straight tubes that can be either vertical or horizontal. The tube appears very close to that of a pipe. Boilers with vertical tubes usually are limited to a maximum of 15 bhp (boiler horsepower).
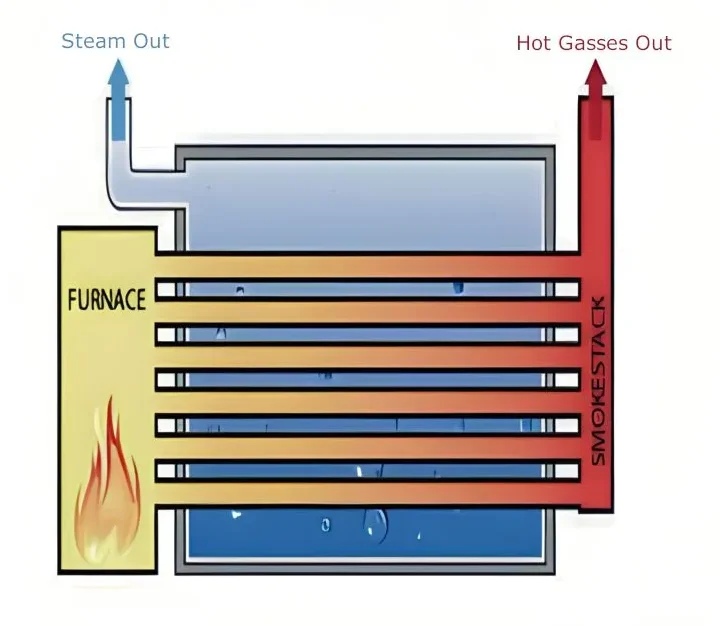
Another term used with fire-tube boilers refers to the number of times the hot gases are passed through the tubes.
Vertical boilers usually have only one pass-through and are called single-pass (fire tube) boilers. A standard horizontal boiler has two passes. The second pass is called the “return flow.” Often this type is called “horizontal-return tubular boiler” (HRT). This type of boiler is internally fired and needs no additional brickwork for a fire box.
Installation of the HRT boiler is relatively easy. Its tubes can be removed from the front for simple maintenance. Due to the large diameter tubes and large steam area, it will produce an additional reserve of 40 percent or more steam for peak loads with only a small loss in efficiency.
Due to the large volume of water surrounding the fire tubes and its (small) five square feet of heating surface per bhp, it is slower than a water tube boiler to reach full steam pressure. Easy to remove front and back plates give quick access to tubes for inspection and cleaning.
A special design, the modified HRT fire-tube boiler features a large amount of heating surface (10 square feet per bhp) which permits a steady, even distribution of heat to the boiler’s water. This creates greater efficiency and reaches full steam pressure faster. Its large combustion chamber is fully lined with thick firebrick and is not quickly affected by lime and scale deposits. This author had a 25 bhp modified HRT boiler in a package plant back in the early 1950s, and it gave excellent service with no operational or maintenance problems even when over firing several bhp for high demand production.
Some boilers have more than two passes and are called “specialty boilers” or “packaged Scotch marine boilers.” In a three-pass fire tube boiler, the stack is located at the rear.
This boiler is available as a “dry back” or “wet back.” The dry back has a rear door refractory and refractory baffles between the tube sheets. The wet back has no refractory rear door or refractory baffles to replace or maintain. The wet back has independent tube sheets with uniform temperatures.
Three and four pass dry back boilers have tube sheets with large temperature variations that could result in premature tube failure and cracks in the tube sheet.
Most fire-tube boilers will have economizing baffles or “turbulators” inserted in the tubes to increase turbulence in hot gases in order to increase heat transfer and clean soot from its tubes.
This boiler has a heating surface of five square feet per bhp and its efficiency is a little more than a two pass boiler. This author had a three-pass Scotch marine 150 bhp boiler with turbulators and steam-applied tube soot cleaner apparatus. The fuel was #5 oil, and propane gas was used for ignition. It performed very well, but required a little more service and maintenance than most HRT boilers of smaller size. It could over fire to more than 20 bhp upon high demand.
Water-tube boilers
A water tube boiler has the water, not the hot gases, inside the tubes. The hot gases surround the tubes and heat the water inside. Since less water is contained in a water tube boiler, these boilers are very quick steamers and can reach full steam pressure in about l0 minutes to 15 minutes depending upon size and load demand.
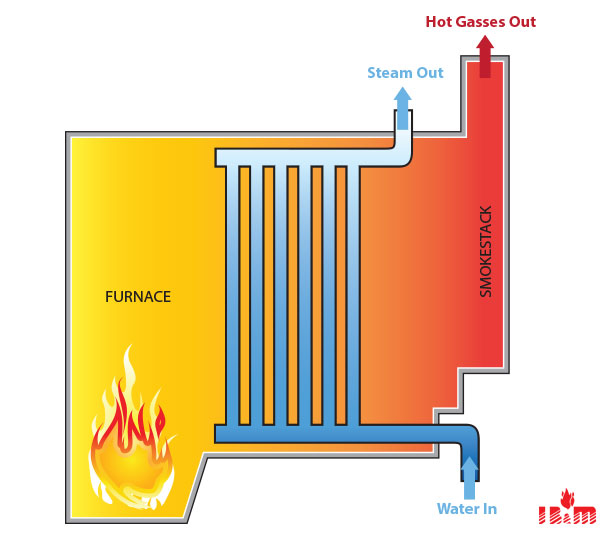
Due to the design, the water flow is not impeded by the tubes and the flow is faster, thus making the transfer of heat more efficient. Having less water and a faster water flow accounts for needing only eight square feet of heating surface to equal one bhp.
The inside of a water tube boiler consists of either bent or straight tubes that are inclined at an angle.
The simplest type of water tube boiler is called a “longitudinal drum boiler.” The drum that is connected to the water tubes runs the length of the boiler. In a cross-drum boiler, the drum goes across the width of the boiler.
A third type of water tube boiler, the “vertical steam generator,” requires less floor space but generally has a lower bhp output.
In some cases, water tube boilers will produce up to 500 percent of their rated capacity. However, the initial cost of a water-tube boiler is higher due the all-steel construction. When shipped disassembled for field erection, instead of being packaged at the factory, the installation cost is higher. This author had a longitudinal drum water-tube 17 bhp boiler which supplied steam to several hot water heat exchangers and served as a back-up for another larger boiler. It over fired with ease and with very little maintenance.
The “balanced packaged water tube boilers with bent tubes” are of the two-drum, multi pass water tube type with five longitudinal gas passes separated by tangent water wall tubes to ensure maximum gas travel. The tubes are press-fitted to the drums using a ferrule attachment welded to the end of each tube. They are easily replaced by tightening a collar. All the boiler components are bolted together to provide easy maintenance and assembly.
The tubes are symmetrical to ensure fast, uniform and balanced circulation throughout the boiler with maximum heat transfer and operating efficiency. Overall efficiency is in excess of 80 percent. The symmet4rical arrangement makes for a very compact water tube package and requires a minimum of space in the boiler room.
With its very large combustion chamber, the water tube packaged balanced boiler will produce the lowest NOx emissions. The burner is very long-lived, and it has a very low Nox emission capability. This is most important since EPA requires a limit of emissions now.
Thermal shock is virtually eliminated due to the multi pass water tube design with symmetrical tubes. Balanced flow and heat transfer is capable of operating with temperature differentials up to 150 degrees F. Most manufacturers warrant the pressure vessel against thermal shocks for 20 years.
Natural circulation of the water in the tubes is accomplished by two large down-comers (large tubes at the front end and rear running vertically), no external circulating pumps are required. Full steam pressure can be reached in about 10 minutes.
One configuration of a water tube boiler has flexible, balanced tubes that can be individually removed. With sectional tubes attached by unions, sections can be easily and inexpensively replaced through the cabinet doors with minimum down time. A built-in return system is available as an option.
Tubeless boilers
Tubeless boilers have become very popular among smaller operators. Their popularity is due to their simplicity in operation and maintenance with little chance of error in blowing down too long and repairs are simple.
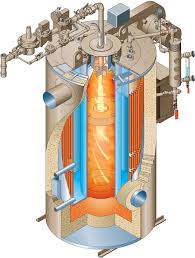
The tubeless boiler is a vertical type with the burner located either at the bottom, middle or top. It has no tubes since the steam is collected over the water in a large jacket or “U” tube.
The gases pass through the combustion chamber giving off their heat to the jacket. Convection is accomplished in one model by a series of circular steel rings around a stainless steel baffle. Hundreds of U-shaped steel rings are the conducting fins, spot-welded to the surface of the furnace wall. A cylindrical stainless steel baffle forces the fire to flow through the heat conductors which gather and transfer heat to the water.
Another model uses extended surface fins attached to a heat exchanger above them with a three-pass design.
Still another model uses the power burner to deliver a spinning flame down the length of the furnace. The hot gases from the flame are carried upward in the secondary flue passage and over the convection fins which are welded to the full length of the vessel. These fins transmit the remaining heat into the outer side of the water vessel. This is a two-pass boiler. The power burner is located at the top of the boiler. The water levels are controlled by three rods that act as probes at different levels. This boiler operates at about 80 percent efficiency.
After the combustion chamber, the gases pass around the jacket, imparting their heat to the water in the jacket before leaving the boiler. The water and generated steam will be inside the jacket, surrounded by the available heat from the fuel. This author had this type of tubeless boiler for over 15 years. The main problem was steam siphoning caused by corrosion in the baffles behind the water-level control component. This boiler must be blown down and treated religiously, especially in areas with water hardness over one grain.
