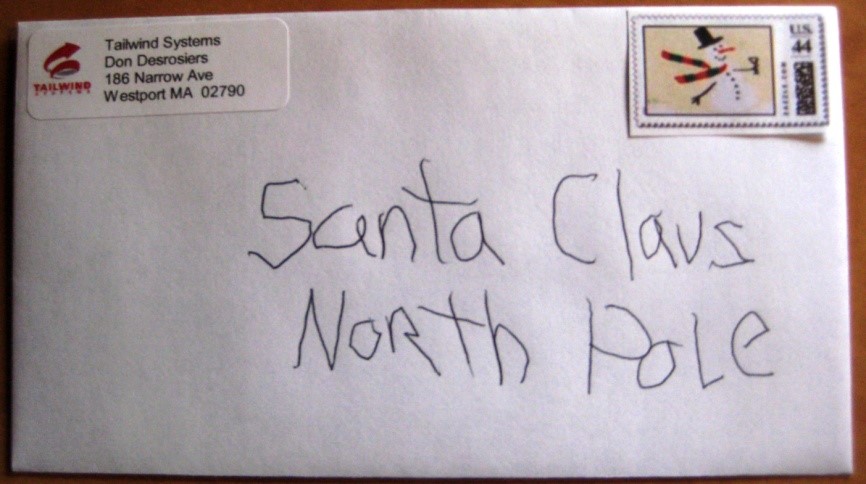
When I expanded my business into India, I was quite impressed with the focus on presentation of finished goods; the packaging. I said this before, when I wrote about my experiences in India; I was so enthralled with how great my clothes looked that I didn’t unwrap the last shirt for over a year. It literally looked better than new.
I have at least one client that is a boutique cleaner, and they could teach all of us a whole lot about packaging. Many garments are returned to the customer in decorator boxes. “Better than new” is an understatement.
But this isn’t what I’m asking Santa for. This sort of packaging already exists. What I’m thinking of is a line packaging for all type of garments that raise our level of professionalism to new heights. The folded shirts from India were folded over a cardboard that was much larger than what we see here. I guess about 9 inches wide and 15 or 16 inches tall. This was covered by a crystal-clear wrap that was somewhere in between cellophane and poly. And the cello-wrap fit snugly over the shirt, resulting in a package that was durable. You can’t toss around a folded shirt that’s been packaged here. It would easily fall out of the loose bag and fall apart. Not so with a shirt that’s been securely packaged. You could toss it around a room, for sure, but more importantly, such a package could travel in a suitcase around the world and still look better than new. I know, because I’ve done it. As a bonus, the image enhancement would be unparalleled. This industry needs a full line of affordable but effective new ways to present our hard work. Let’s get out of the box!
I have tried hard, but I cannot warm up to the way that blown-sleeve shirt units deal with short-sleeve shirts. The answer isn’t that far away. The built-in short sleeve devices aren’t quite right. Some of them deform the sleeve, some of them snap out of the device during pressing, some are simply ignored and the sleeves are finished with an iron in the touch-up area. There is a compromise, but the cost is considerable. If you want to do a quality short sleeve shirt, follow these steps:
-
- Press the collar in the usual manner
-
- Lay one of the sleeves on the collar buck carefully, making certain that the fabric is flat and aligned and that the seam is straight.
-
- Lower the steam chest for exactly 5 seconds. That’s about as long as it will take to prepare the other sleeve.
-
- Release the press head, remove the first sleeve and place the other one
-
- Press that sleeve for exactly 5 seconds
-
- Release the press head and the shirt is ready to be finished on the body press.
The sleeves will be ready to press, but not ready to wear. The fabric still has substantial moisture remaining in it, but that moisture is trapped inside the interior of the individual fabric fibers. Only the outsides of the fabric are truly dry. If this sleeve were left like this for some time, the dry parts of the fabric would wick out the moisture and spoil the appearance of the garment. But that’s hardly the plan. The crease that you made is subtle, and the two halves of the sleeve are NOT stuck together. If they are, they were pressed for too long.
Now the shirt is finished on the body press, but the short sleeve attachment is not used. Hot air is forced through the sleeve, drying the fabric from the inside out and the sleeve crease is dulled. You will have a well-pressed sleeve that is not misshapen.
So the wish is to make this all much easier and doable in one step. We need a completely redesigned collar/cuff press. To make this happen, the following is required:
-
- The steam chests that press the collar must be separate from the cuff heads
-
- The press must be designed in such a way that the cuff bucks are large enough and suitable for pressing a short sleeve.
-
- It must be possible to press the collar and the short sleeve simultaneously, so the press needs to be compact, and I imagine that the steam chests for the cuffs need to be on top of the collar chests. This design is not new. Itsumi has a stacked collar/cuff press with the cuff unit on top. Sankosha has a stacked collar/cuff with the collar unit on top.
-
- This press, however, will require a short sleeve cycle that will release the steam chests from the sleeves after 5 seconds
So the short sleeve shirts will be handled routinely. Just like the long-sleeved counterparts, the shirts will start at the collar/cuff machine. Long sleeves will be done in the usual manner using the default long sleeve cycle, but the short sleeved shirts will be done differently. The presser will lay the collar on the buck and lower the press head. Then, the presser will prepare the sleeves, and lay them on the press and lower the head, but this time using the short-sleeve cycle, which presses the collar for 30 seconds but the sleeves for only five seconds. Afterwards, this shirt is simply queued up for pressing on the body press, and you can do them quite quickly because there is no sleeves or cuffs to deal with. This is a big present, but I really want this.
Most of you have a button sewing machine. But there is a big problem. The hole in the needle is about one-tenth the size that it used to be when I was 20 years younger. Damn those needle-makers! If you get a cheap travel sewing kit, oftentimes you will find a needle-threading gadget in that kit. It’s just a small piece of metal with a very thin but stiff metal hook attached. This thin wire is easy to snake thru a needle hole, allowing you to then place the thread into the protruding end. Pulling the device out of the needle hole pulls the thread along with it. Wawak Sewing Supply sells these for 35 cents. I should buy a few hundred dozens of these to carry with me so that I don’t show my age so readily whenever I am near a sewing machine. But my Christmas wish is a bit different…an extension of this simple but effective idea. Sewing machines need to have a similar device built in. Sure, it can be this device, somehow tethered to the machine, gee, you don’t need to wait for Santa Claus for that! But suppose the sewing machine had a gadget that performed the same task, probably somewhere behind the needle. Perhaps when a needle needs threading, you would simply reach behind the needle, slip this device into the needle, then the thread into it and, Voila!
By the way, Cleaner’s Supply has it too:
http://www.cleanersupply.com/products/product.cfm/pid/10902/Needle-Threader-Standard-1pk/
Honestly, this can be the single highest return on investment of any labor saving device or idea that I have ever come up with:
It takes 7 minutes to fight with a sewing machine in an attempt to get that super-slim thread into that microscopic hole. At $12 per hour, that means it costs you $1.40 every time that machine gets unthreaded. This happens 300 times per year, so we are talking about $420 a year to thread a needle! The ROI is less than 2 hours!
Now Santa, quit jerking me around…I didn’t get a mini-bike, a train set or that wristwatch packed in water. Give me this stuff, will ya? I made it easy this year!
“If you do what you’ve always done, you’ll get what you always got.”

Donald Desrosiers
Don Desrosiers has been in the laundry and drycleaning industry for over 30 years. As a management consultant, work-flow systems engineer and efficiency expert, he has created the highly acclaimed Tailwind Shirt System, the Tailwind System for Drycleaning and Firestorm for Restoration. He owns and operates Tailwind Systems, a management consulting and work-flow engineering firm. Desrosiers is a monthly columnist for The National Clothesline, Korean Cleaners Monthly, The Golomb Group Newsletter and Australia's The National Drycleaner and Launderer. He is the 2001 winner of IFI's Commitment to Professionalism Award. He has a website at www.tailwindsystems.com and can be reached at tailwindsystems@charter.net or my telephone at 508.965.3163