Some plant owners seem to be too busy to run their plants. They get caught up in the day-to-day trials and tribulations. They are the quintessential, text book reactive managers. This happens because they are behind the error curve. An elementary example of this is the manager that spends a disproportionate amount of time dealing with the end result of, say, poorly pressed shirts. Employees are hired and trained to inspect and touch-up. Customers are complaining, so he needs to massage them. Shirts are unwearable, so they need to be rewashed and repressed. Complaints lead to refunds. Dissatisfaction climaxes and customers are lost, therefore dwindling piece counts need to be addressed, one way or another. If a careful analysis ever does take place in order to isolate the root cause of the problem, at times it is found to be something that is far, far easier to remedy than dealing with what that problem has caused – customer dissatisfaction. If you are dealing with the problems caused by poor quality, perhaps the real problem was that an employee needs to be re-trained, a wrench needed to be turned or a pad needed to be replaced. But a manager caught up in the vortex of attempting to cure symptoms while in the midst of mounting operational issues, doesn’t see the root causes of problems. He only deals with the results. We commonly refer to this as a firefighter.
It is difficult to see the minutia, much less, deal with it. It takes a skilled manager to always seek out the root cause of a problem. It often requires a manager that has skills in every job in every department. I am able to accept that some managers will never have this skill set and will need to rely on the competence of their staff for certain things. Still, I see evidence that managers run their plants with blinders on. It’s hard to understand what you see in Photo 1. This is not an anomaly. I have seen this and photographed it several times. Allowing this is a result of being so caught up in the big picture that you no longer see the details. I hear managers say, all too often, that they don’t worry about the little things. They admit to looking at the big picture, only. This is hazardous. Every procedure, in every department, exists for a reason and its enforcement is critical.
Read this column as a whole with this adage in mind: How do you prevent big problems? Take care of the little ones!
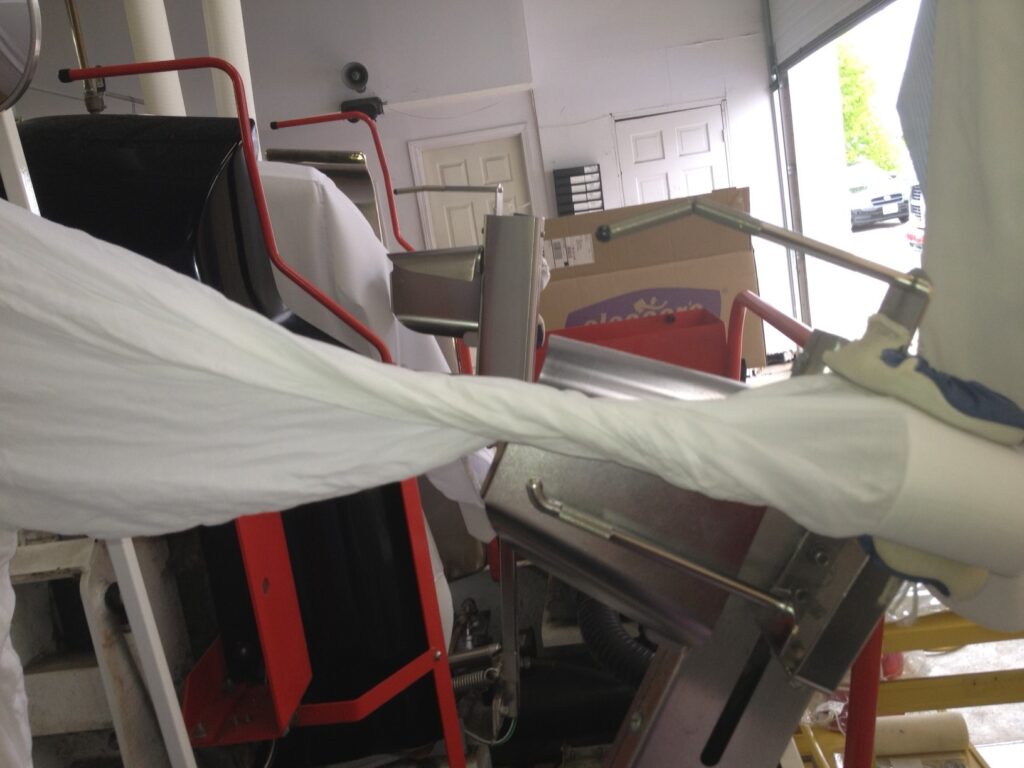
I can’t be sure what happened to the pictured shirt. Was it repressed? If so, the result was reduced productivity. Was it sent to touch-up? If so, unnecessary effort and labor is a direct result. Was the presser corrected? If so, follow-up supervision is essential. If not, there is little guarantee that this will not recur.
The key is to go back to basics. Understand the need for the details and underscore their importance. Every procedure has a reason and every detail contributes to the bottom line in its unique way. “If you do what you’ve always done, you’ll get what you always got!”

Donald Desrosiers
Don Desrosiers has been in the laundry and drycleaning industry for over 30 years. As a management consultant, work-flow systems engineer and efficiency expert, he has created the highly acclaimed Tailwind Shirt System, the Tailwind System for Drycleaning and Firestorm for Restoration. He owns and operates Tailwind Systems, a management consulting and work-flow engineering firm. Desrosiers is a monthly columnist for The National Clothesline, Korean Cleaners Monthly, The Golomb Group Newsletter and Australia's The National Drycleaner and Launderer. He is the 2001 winner of IFI's Commitment to Professionalism Award. He has a website at www.tailwindsystems.com and can be reached at tailwindsystems@charter.net or my telephone at 508.965.3163