The water separator is the one common component of the following pieces of drycleaning equipment: reclaiming tumblers, stills, muck cookers, and most vapor adsorbers. Each of these pieces of equipment has a water separator as the collection point for the solvent/water flowing from the machine. The purpose of the water separator is to allow the water/solvent mixture leaving the condenser to flow into the separator and settle, so that pure solvent may be returned to the base tank of the drycleaning machine for reuse, and the water drained to a collecting point.
Basically, there are two types of water separators – the open top unit and the sealed unit. The advantage of the open top unit is accessibility for cleaning and maintenance. The internal working parts of both units are essentially the same. Water separators are simple devices consisting of a water separator (container), with an atmospheric vent, three pipe connections, one or two inside baffles, and no moving parts.
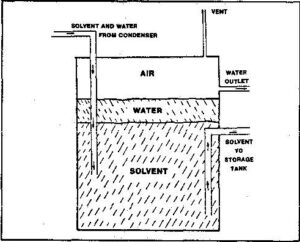
Figure 1 is a typical water separator used for perchloroethylene. In both cases, the ater/solvent mixture leaves the condenser and flows into the separator where the lighter liquid (water) floats to the top before running through the upper pipe to the water collecting point. The heavier liquid (solvent) drains off the bottom through the pipe to the base tank of the drycleaning machine. The water separator works on the difference of the specific gravity of the solvent and water. To operate correctly, the vent line must be free of obstructions.
New or just cleaned water separators are put into operation by filling the separator with solvent to the solvent drain level. Then, a small amount of water is poured into the middle of the separator (container) and not between the solvent outlet line and the baffle closest to it. This procedure is called priming. If the solvent from the water separator is cloudy, a rag filter is often added to the system to remove excess water. The rag filter would be added to the system in the solvent line between the water separator and the base tank of the drycleaning machine.
Petroleum machines do not have water separators. The still does have a moisture absorber to remove the water from the petroleum. The moisture absorber consists of a rag filter (container) filled with cotton fabric. The distilled solvent is pumped from the petroleum still to the clean solvent storage tank via the rag filter. The water is drained from the bottom of the container to the collecting point and the petroleum goes to the solvent storage tank from the top.
Problems
As with all equipment, regular inspection and cleaning is extremely important. Neglect can cause the water separator to malfunction, and numerous problems can result. Some of the common problems are:
- Bad Solvent Odor: Fungus growth can occur in the water layer, causing the water drain to clog and produce a bad odor. Excess dirt and lint from the condenser may also pass to the separator, causing a clogged outlet and odor. To correct this problem, clean the condensing coils, the separator, and the clogged outlet.
- Solvent in the Sewer: Help prevent this by keeping the bottom of the water separator clean and free of rust and scale. If the bottom of the separator is raised with debris, the level of the solvent may raise to the point that solvent goes out the “water outlet” pipe. A solvent detector is available that sounds an alarm when the water leaving the separator contains a high amount of perc. An easy test to see if your water separator is working effectively is to collect some of the wastewater in a clear glass jar. If any perc settles to the bottom after standing overnight, the separator needs maintenance. Flush out the debris with water and then blow out and dry with an air hose.
- Water in the Storage Tank: Water may go to the base tank if the solvent level gets below the “solvent to storage” pipe. To prevent clogging, clean all pipes and the vent.
- Solvent/water Will Not Flow Into Separator: Blockage of the solvent line from the condenser is usually the problem. Clean the lint and dirt from the line and the condensing coils.
- Excess Water in the Water Separator: Check the condensing coils for leaks (usually pinhole in size).
- Solvent Coming From Separator Is Hot: The solvent was hot before entering the water separator. Check the machine the separator is connected with for overheating.
- Boil Over From Still: Residue from the still comes over with the solvent/water mixture in any boil over. Stop distillation and clean out the water separator. This will prevent corrosion in the water separator and contamination of the solvent in the base tank of the drycleaning machine.
Warnings About Water Separators
Some of the following problems with water separators have been repeatedly called to our attention. The listed problems may not only affect your water separator, but the entire operation of your drycleaning machinery.
- No detergent or oil should ever be put in the water separator.
- After a boil over from the still, immediately clean the separator. This will prevent corrosion and possible contamination of the solvent in the drycleaning machine tank.
- Remove any buildup of corrosion and scale.
- Follow the manual for specific cleaning and maintenance instructions for your machinery.
The above problems can only be corrected by routine inspection and cleaning.
Maintenance
Check your machinery manual to establish a maintenance schedule for each of the pieces of drycleaning equipment having a water separator. The maintenance of each separator in your plant should then be on a schedule. Following is an example of an inspection and cleaning schedule for a water separator.
Maintenance Schedule
Water Separator (Perc):
- Daily: Inspect for any problems. Pour small amount of water (open top unit) into center of separator container – just enough water to run out of line to collecting point.
- Monthly: Inspect and clean vent, any clogged line, bottom of container. Check for solvent coming over with the water. Use the glass jar method to check for solvent settling.
- Bi-Yearly: Completely flush, dry with air hose, replace solvent and water layers, Ream all lint, dirt, and/or rust from the vent or lines. After maintenance, check separator for
- performance.
Moisture Absorber (Petroleum):
- Daily: Inspect and clean after each use. Launder and dry rag filters. Store rags in closed, dry container.
- Monthly: Inspect drain. Inspect pipe to distilled solvent tank. Inspect laundered, filter rags for wear and odor. Check for odors. Check for solvent leaks.
Summary
The water separator is one of the simplest units in your plant, but it may frequently fail to perform properly if poorly maintained.
IFI’s recommendation is that disposing of separator water to the sewer is the least environmentally sound method. For further information and alternative methods of disposal, with pros and cons, refer to Hazardous Waste bulletin, #11 (HW-11).
This article is from DLI’s TOI-621
